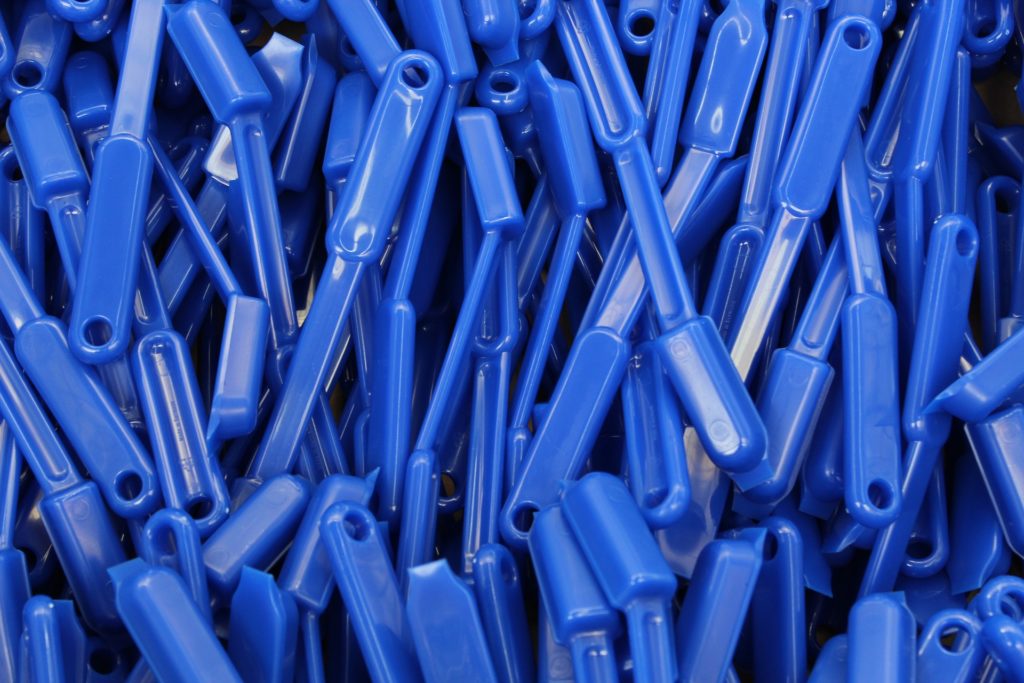
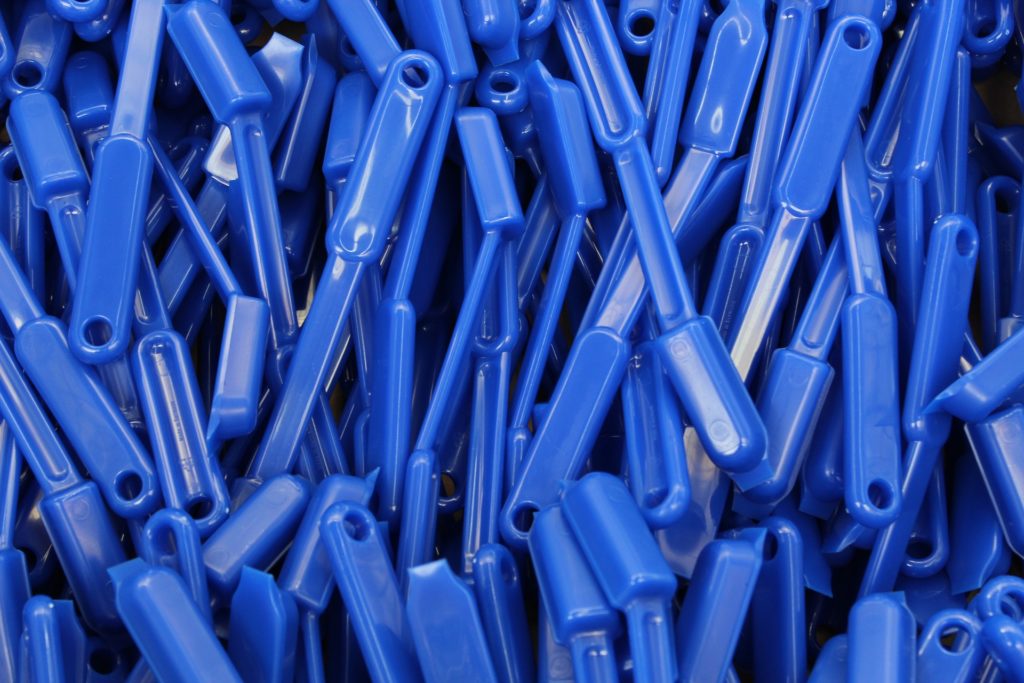
Injection molding has been the go-to solution for plastic manufacturing. It has been the first option for mass production plastics for many years. A vast number of products we use or see every day around the world are produced via plastic injection molding.
However, the molds required for injection molding are usually made of metal and tend to be very expensive and time consuming to manufacture. These are two downsides for anyone looking for fast and low-cost production, especially in the highly competitive world we live in.
How can 3D printing help?
In the past 3D printing technologies did not provide a good enough surface finish and precision. They were also made from materials that did not stand up to heavy use. This is why 3D printing has mainly been used in the prototyping phase of product lifecycles. However, with the latest developments in printing technologies and materials, 3D printers can achieve a much better surface finish. And the materials are much more diverse.
With these advances, people have been testing out 3D printed plastic molds for low volume production.
These new capabilities of 3D printing make plastic molds a great alternative to the traditional metal molds. Among the main capabilities of 3D printing for injection mold making, the most relevant are:
- Reduced investment compared to machined metal molds.
- Reduced costs deriving from materials.
- Faster turnaround times.
- Faster and cheaper design changes and iterations.
- Intricate and more complex geometries are possible.
- Beginners can start their own small-scale manufacturing business.
Can I make injection molds with any 3D printing materials?
Currently, there is a wide variety of 3D printing materials available in the market, but not all of them are a good fit for making injection molds.
The process of injection molding is a rigorous one. It requires the mold to resist significant temperatures changes. In addition, getting the product out of the mold sometimes means a lot of manipulation, which could result in the deformation of the mold if the material does not have the resistance required.
Also, the material you use should be able to be shaped into the highest level of detail, since injection molding requires high precision and smooth surfaces from the molds in order to achieve very tight tolerances.
A good choice of material to 3D print molds is the variation of acrylonitrile butadiene styrene (ABS) known as “Digital ABS”. This material provides the same properties as the standard version, but it has improved impact resistance for parts that are exposed to hitting and shock. Of course, high-quality surface finish and resistance to high temperatures are also provided by this version of the ABS.
Can I always use 3D printing for injection mold making?
Unfortunately, this technology still isn’t perfect. There are some situations where using 3D printing for injection mold making may not be the best ideas, as there could be some drawbacks.
For example, the effectiveness of 3D printing molds is limited to a low number of batches, so if you are planning to produce large numbers from the get-go, you should better consider this aspect, as you may end up having too much work without the expected reward.
Also, keep in mind that 3D printing materials are still less durable than those used in traditional injection mold making. Therefore, even when you use the most durable printing filaments, the durability of your molds will not be the same as the durability of traditional industrial molds.
However, there are some ways to improve the probability of success when using 3D printing for injection mold making. Examples are considering how to make a design to help you ease the manufacturing process and using other materials to increase the strength and provide support to the mold. Anyways, in case of doubt, do not hesitate to contact us.
info@hlhprototypes.com
HLH, we make things for you