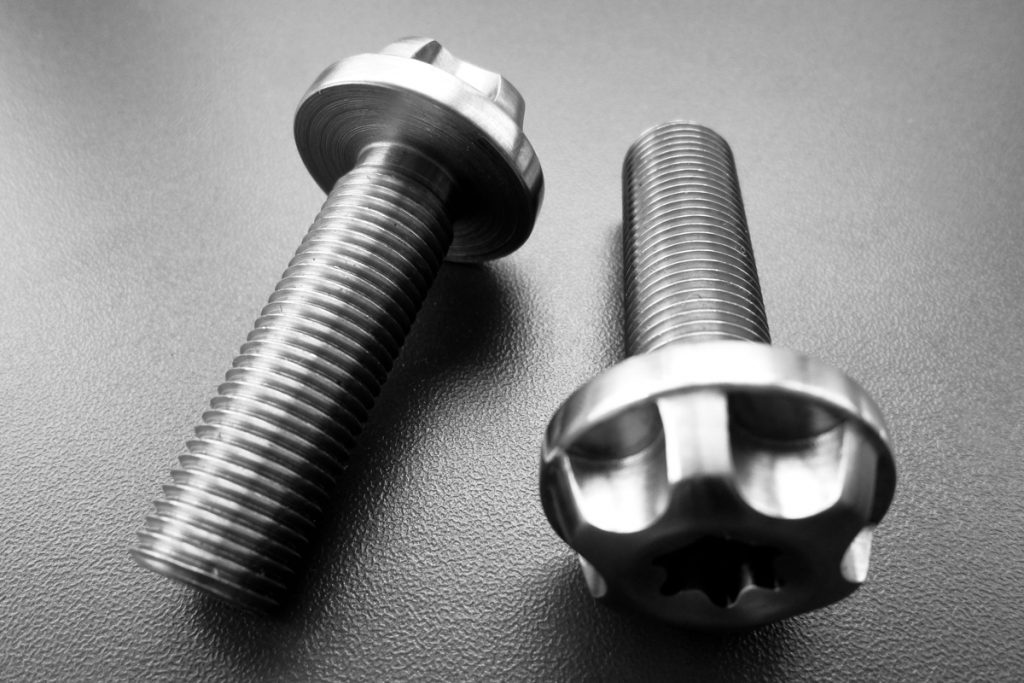
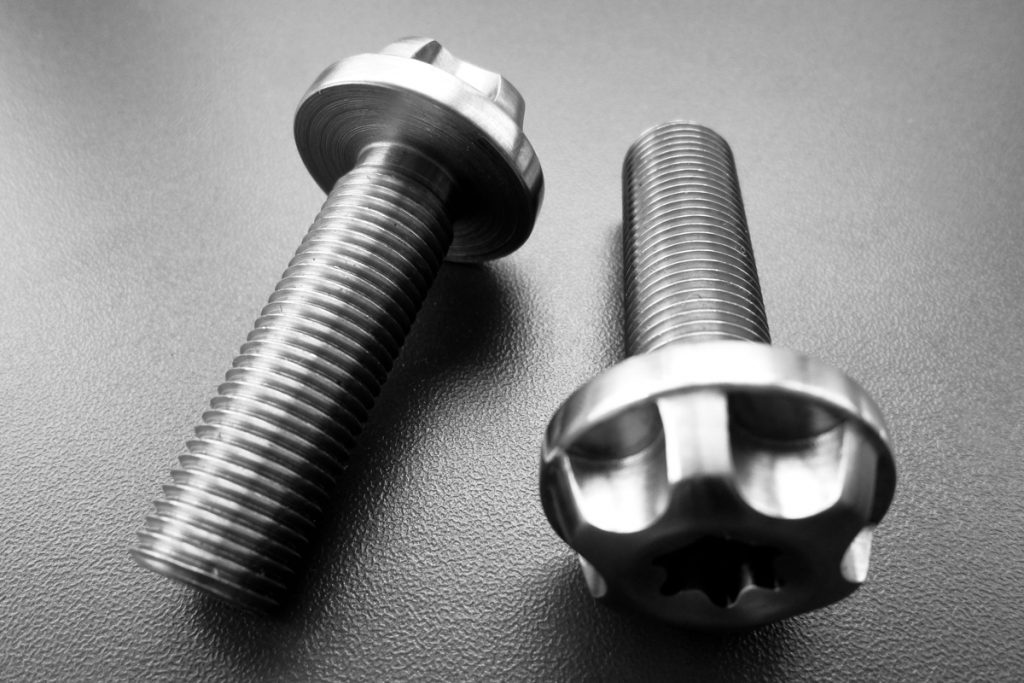
CNC turning is a computerized process that uses a lathe to make circular cuts into a spinning material. The automated CNC process gives a more consistent and precise product than manual machining can achieve, especially with highly detailed designs. This is an efficient method for machining prototypes or other custom-made parts.
CNC stands for “computer numerical control” and includes many options for computer-automated subtractive machining. CNC machines follow pre-programmed commands to cut a piece of material into a specified shape. The program in usually written in G-Code, the same language used by 3D printers, which can also be generated using models created in CAD software. The G-Code allows for flexibility if you ever need to alter your design.
Cylindrical components are easily machined using CNC turning. The computer-controlled machines are most often used to make precise cuts on outer surfaces. However, depending on the capabilities of a given machine, you can also create tapered surfaces, shape the inner surfaces, etc. The turning process works on many materials, including woods, metals, and plastics. When using CNC turning, it is important to consider the outer diameter (OD) of your material. Many CNC turning devices have a maximum OD that they can process.
Depending on your project, CNC turning may not be the best option. For components with flat surfaces and non-circular cuts, CNC milling would be more helpful. For some parts, you may want to use a combination of both CNC turning and milling.
Understanding the capabilities of CNC turning will help you determine how to best utilize it. Its computerized process allows for precision and easy adjustment to design. CNC turning is an excellent option for flexible, high-quality prototyping.