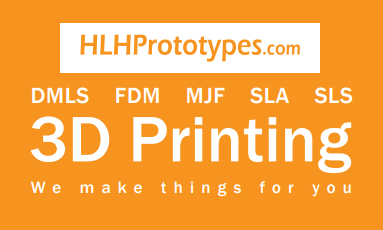
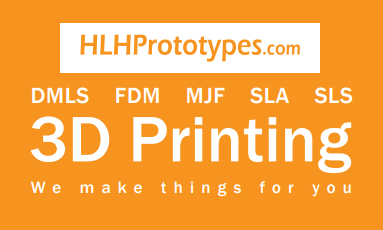
While 3D printing has been taking an important place in manufacturing in recent years, this technology has also been considered cost-effective only for a group of niche products and prototypes. The main reasons include that additive manufacturing technology still struggles with the consistency needed to manufacture for certain industries.
Fortunately, Industry 4.0, deemed the new industrial revolution, brings with it the development of innovative solutions such as cloud computing, simulation, IoT, edge computing, big data, analytics and augmented reality, all of them being applied to optimize manufacturing processes. We can also add “digital twins” to this list.
What are digital twins?
A digital twin can be defined as a virtual replica of the product. It starts as a 3D model that is exactly the same as the physical version of the product. The main characteristic of a digital twin is that it allows analyzing real-world data and real-time monitoring of the physical product even after it has left the factory, and it is operating in the field.
The data is collected by means of sensors on the physical version of the product and it is then sent to the digital twin to study the behavior of the physical twin. By using this practice, it is possible to:
- Understand the operation of products and production lines.
- Prevent accidents.
- Predict asset downtime.
- Optimize products.
Digital Twins in 3D printing
3D printing is evolving fast and there are more and more materials that can be 3D printed. However, some materials may suffer distortions along the printing process. In addition, many 3D printed parts must be qualified and this usually means a long trial and error process, which results in increased cost.
To avoid all these inconveniences in the 3D printing process, digital twins can be used to simulate the manufacturing process and identify whether there will be distortions and where they may occur, so they can be corrected on the 3D model. This results in a new model that is fully optimized to compensate the discrepancies and obtain the best possible printing results.
The simulation deals with problems that may appear from the focal melting of individual printed layers as a result of the heat generated during 3D printing.
Moreover, simulations on the digital twin can reduce the number of trial and error tests required to validate the product-specific requirements and to qualify the components, making the whole process, even more, cost-effective.
Finally, manufacturers can take advantage of the digital twin concept by creating and saving 3D printable files of replacement parts that may be needed in the future or during critical situations. This allows solidifying continuous manufacturing operations as original components can be easily accessed whenever they are required.
In other words, digital twins consisting of mechanistic, control and statistical models of 3D printed parts combined with machine learning and big data can provide the following benefits to 3D printing manufacturers:
- Reduce trial and error testing
- Reduce possible defects during print
- Shorten the time between the design and production
- Increase consistency between parts
- Highlight possible problems
To discuss your 3D printing projects talk you our team today
info@hlhprototypes.com
HLH, we make things for you